Is the Factory of the Future Full of 3d Printers?
As discussed in the article “Is Serial Additive Manufacturing Taking Off?”, the Additive Manufacturing world has seen significant growth in the past few years. Every year faster, more accurate technologies are being presented. AM knowledge is more accessible. New materials and post-processing methods are developed and implemented. To make it possible to use all of that in the production environment, we are also working very hard to introduce qualification processes to meet the highest requirements regarding part quality, production repeatability, and many other aspects.
What Will the Factory of the Future Look Like?
The question that many companies in the market ask today is “What will the factory of the future look like?” Today's decisions are going to impact the next few years, and they need to be made wisely. Investments to implement and qualify the new technologies, adjust the object design to specific requirements and set up processes can be significant.
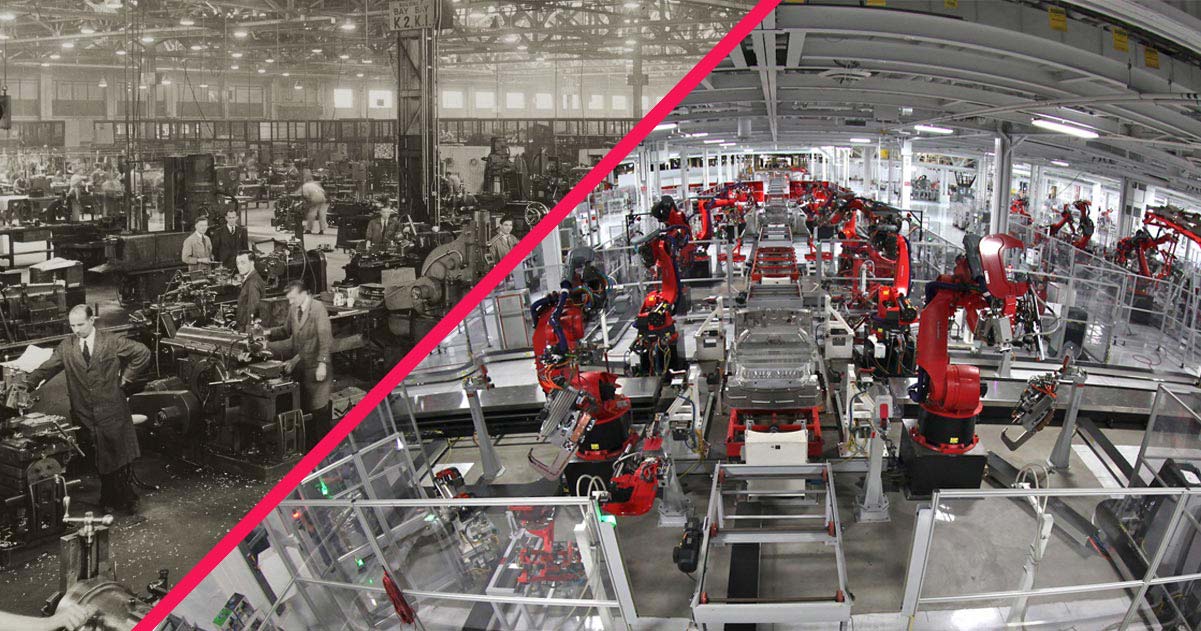
Let’s start with the big picture, and a bit of history. One of the most important turns in the history of production management was the well-known Toyota’s Lean Manufacturing concept. What is lesser-known is that, when lean manufacturing was introduced in factories, managers used to focus mainly on the utilization rate of each machine. Factories were basically designed to keep running at full capacity. From the viewpoint of the machines, it is efficient, but from the perspective of the factory as a whole system, it is widely inefficient at times. AM - and the Agile Manufacturing concept it carries - is probably facing a similar challenge. AM is a capital-intensive technology, and most of the companies are looking to fill their platforms to reach their ROIs. The questions that still widely remain to be answered are, what do we really need to print? How often are we going to switch the products? Make or buy? How do we integrate the 3D printing process in overall manufacturing value chains? These questions are even more relevant in a post-COVID world.
Our conviction is that the factory of the future will be customer-centric on one end, enable better flexibility and interoperability, and on the other end, will tap into the supply chain benefits of AM, meaning: reactivity, decentralization and flexibility.
Based on our experience with world leaders in different sectors as our customers, we’ve established a logical growth strategy for implementing the AM capabilities inside of the factory.
The first question we need to answer is - what do we need to produce, and how do we want to do it? There are dozens of available manufacturing technologies in the market. To get to the point where we will have the production environment ready, we should analyze all of the products at our company and check if they should be produced using AM technologies or if traditional milling, turning, laser cutting, bending, etc. would be more efficient. Our Digital Qualified Warehouse enables us to choose the right parts to be produced using 3D printing. Second step would be to define the qualification processes we should follow. It applies to all of the processes, materials and also end products.
After the Digital Warehouse is established, the first pilot production site can be built. It enables us to test all of the theories we have and bring the first parts. It is important to have a software solution which allows us to track the data to follow the qualified processes and put the quality management system in place. That’s what we call the Agile Factory phase.
Last but not least, the real power comes from the scaled production system. To minimize the logistics and warehousing costs, we want to build factories all around the globe. It is important to connect all the sites within one system and manage their utilization and productivity. That would be the last phase of the AM implementation across the organization, which we call the Distributed Ordering Process. Based on our experience from the previous steps, regardless of the scale of the project, we should be able to follow strict QM requirements, utilize our machines, efficiently as possible, and deliver the products that fit our needs. It won’t be possible without a centralized data management and storage system.
In that regard, the logical starting point should be creating a Qualified Warehouse of AM ready parts, and building the operating model on the applications and end customer technical and economical requirements.
Advantages and Disadvantages of 3D Printing in Production Environment
Does 3D printing have a place in the factory of the future? AM technologies have a lot of advantages. Freedom of design, minimum scrap after production, and elasticity of the produced goods are some of those advantages. We are no longer stuck with one product manufactured in one factory. In theory, each single part might be different from the others.
However, additive manufacturing technologies alone are not enough in many cases. Certain post-production methods are required to remove support structures, clean up the surfaces, achieve given tolerances and apply a heat treatment process. It is also possible to use AM as a step in the production flow. For example, pre-product might be prepared with internal cooling channels, and traditional CNC processing could be applied after. Possible combinations are unlimited.
It is well known that AM has a lot of disadvantages. The biggest problems that we’ve seen with our customers are lack of the qualification processes and norms and slow production times. We hope that the first of these problems will disappear over the next few years, as many of the organizations are working very hard to introduce standardized procedures to qualify processes, materials and end-use products. A lot of the machine producers are trying to speed up the process of AM manufacturing. Someday it might be possible to shorten it and compete with traditional manufacturing methods.
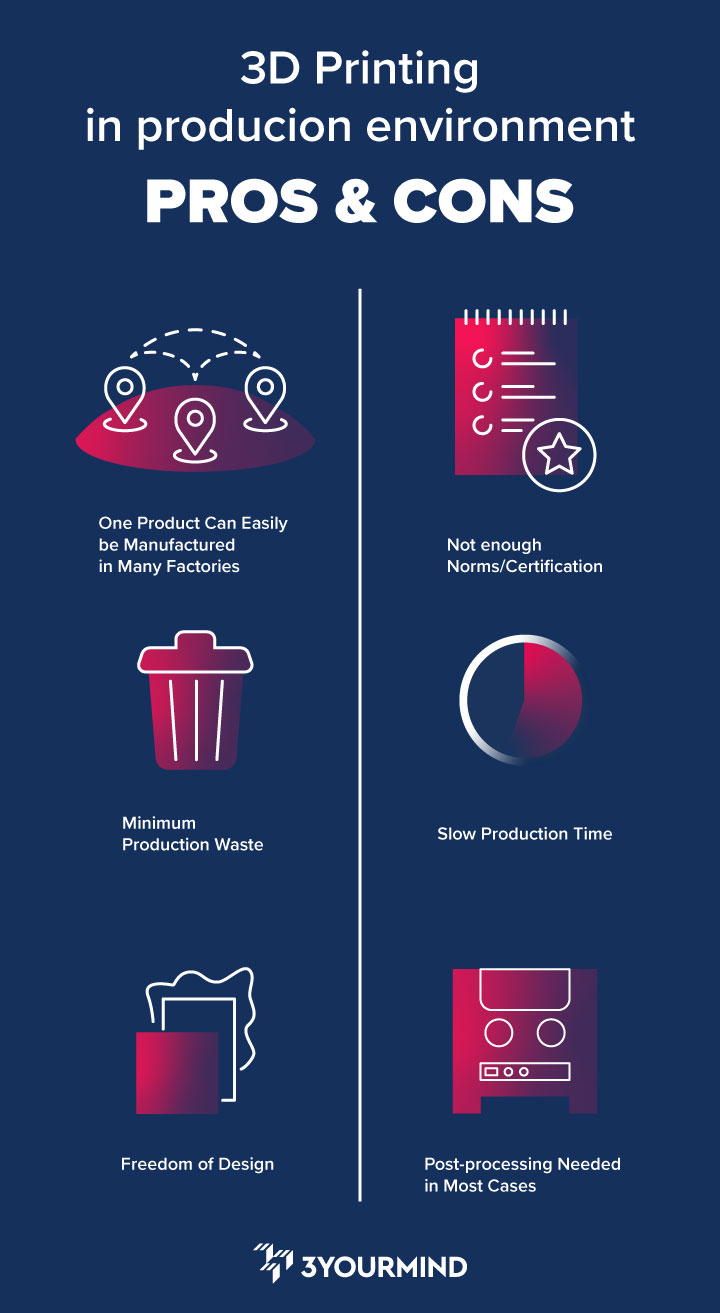
Is it Possible to Make Work Together Smoothly?
The big difference between the production time in AM and traditional manufacturing methods leads us to another problem. Some market segments are based on takt times, which are very short and accurately defined. It is not very easy to use a technology which ends up in a single process after a couple of hours, when other production steps are counted in seconds. One example of where this is a serious problem is the automotive industry.
In our opinion, it is important to change our mindset and think about the production site in a new way. 50 years ago it wouldn’t have been possible to imagine a factory where no people were needed to assemble the end product, because all those manual activities would be taken care of by robotic arms. Today we can’t imagine a production line where no screws are needed, but where each next part is produced on top of the previously prepared assembly. Is that something what we could treat as a normal approach in the next 50 years?
The Factory of the Future is Taking Shape with BMW’s POLYLINE Project
One example of a current factory of the future project is POLYLINE. 15 industry and research partners are working together to rethink the way we produce industrial grade products and automate the processes around it. Today, software automation around the production line is at a mere 10%. Furthermore, automation on the hardware site is at roughly 30% and is one of the key obstacles to make AM a truly competitive production method. The goal of the POLYLINE project is to achieve 90% in both software and hardware automation. The seamless and automated interaction between the physical and digital world will be one of the key accomplishments of this project. That’s why the 3YOURMIND platform is the central data storage and management system for the project. POLYLINE is led by EOS and BMW and is funded by the German Federal Ministry of Education and Research with 10.7M euro.
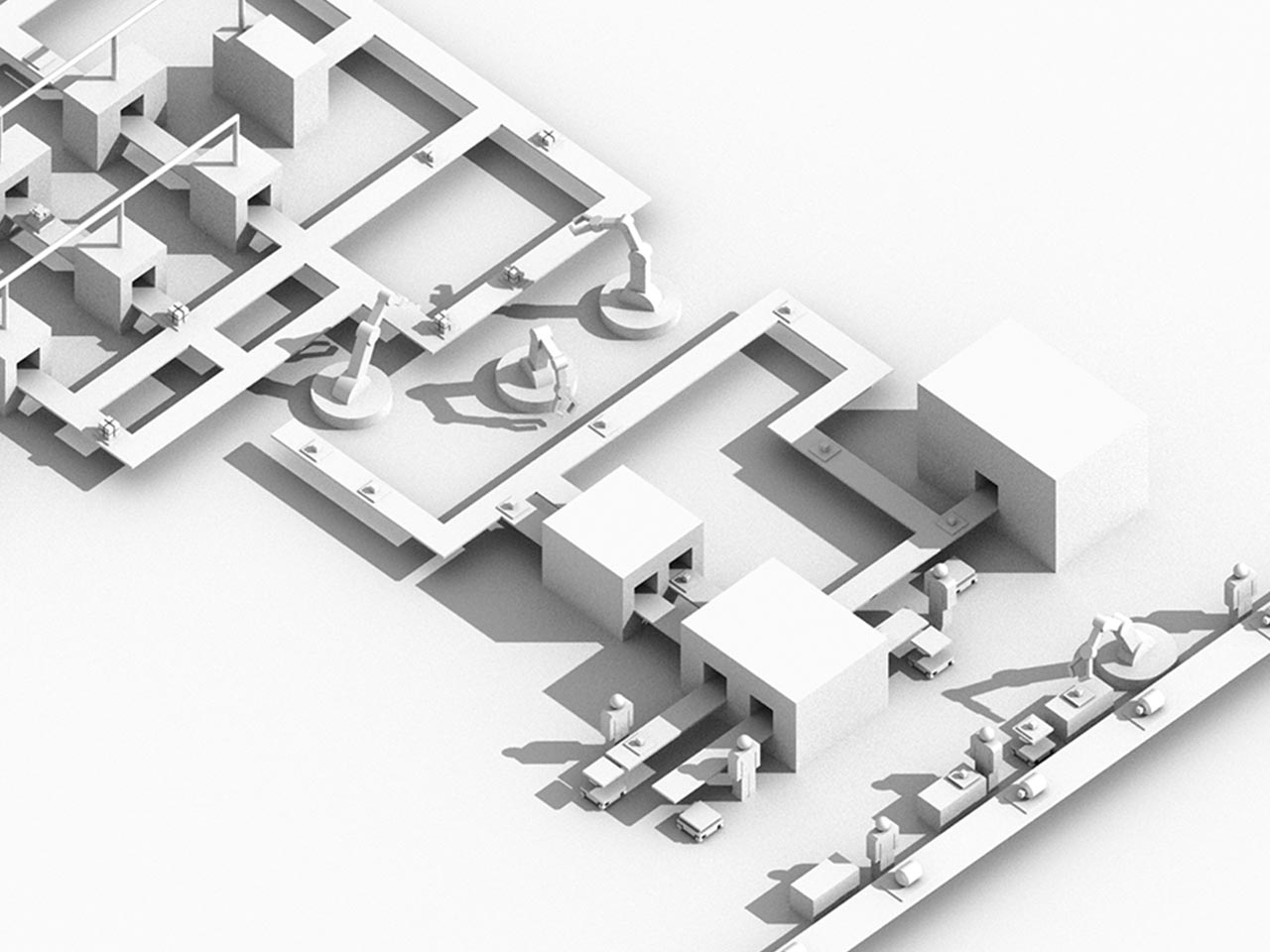
AM Enhances Flexibility for the Factory of the Future
The main goal of the idea to build an innovative factory is to produce the best possible products. We want to minimize the logistics costs and warehousing times. We want to produce parts which are more reliable and eco friendly. To achieve this we need to understand the advantages and disadvantages of all available materials and production methods.
We believe that the factories of the future will be spread around the world. They will be able to quickly switch focus, to enable production of more than a single product. They will help us to deliver parts just in time and in the right place. AM technologies will be used together with the traditional manufacturing to produce lightweight, reliable parts. It will be possible to customize each part separately for the customer’s needs. To control and track all of that, software systems with a direct connection to every single machine will be used.
Want to learn more about how original equipment manufacturers are using additive manufacturing? Visit our industries page.