Frequently Asked Questions About 3YOURMIND Software
Want to learn more about 3YOURMIND software? Browse this resource for answers to common questions.
This guide contains frequently asked questions about 3YOURMIND software. 3YOURMIND offers two software products that address different needs of the additive manufacturing (AM) supply chain.
Click on the links below to view frequently asked questions about each product:
- Part Identification (formerly known as AMPI)
- Distributed Manufacturing (formerly known as ERP + MES)
- General Questions
Have a specific question you don't see answered here?
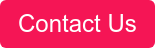
Frequently Asked Questions About Part Identification
What is 3YOURMIND's Part Identification?
Part Identification, formerly known as Additive Manufacturing Part Identifier (AMPI), helps enterprises analyze their part inventory for 3D printing opportunities. It can handle a large-scale, top-down inventory analysis (hundreds or thousands of parts at once) or a more focused, bottom-up screening of individual use cases.
It evaluates part data for manufacturability, using key performance indicators (KPIs) such as cost savings potential, lead time reduction, technical compatibility, and CO2 emissions. This analysis helps companies determine which parts are ideal for 3D printing, allowing them to build a digital inventory connected to 3YOURMIND’s Digital Manufacturing module for managing production orders.
Combined with Distributed Manufacturing, Part Identification creates an end-to-end process for evaluating and managing additive manufacturing data.
Pictured: Part Identification helps users quickly see whether a part is suitable for additive manufacturing based on technical feasibility, economic savings, and custom assessments.
How does Part Identification analyze suitable parts for AM?
Part Identification assesses parts based on specific KPIs your organization defines, such as cost savings, inventory scores, lead time reductions, and CO2 emissions. This helps you identify which parts are a good fit for additive manufacturing.
The tool also performs a technical analysis to evaluate whether a part is suitable for 3D printing. It screens multiple technologies and suggests the best fit for materials, along with redesign recommendations when needed. Parts that score high in either KPI or technical assessments are ideal candidates for further evaluation by AM engineers.
How does the Part Identification know that my business case fits AM?
Part Identification uses advanced geometric analysis and years of industry experience to recommend the best 3D printing technology for your parts. Our database of 800+ printers can be fully customized with your own machines and data, ensuring tailored recommendations that align with your printing capabilities.
The tool also provides design guidelines that help non-experts follow key design rules, making sure parts are printed correctly the first time.
Pictured: Part Identification offers manufacturability checks, which help you compare print feasibility between different technologies and provide optimization suggestions based on design for additive manufacturing (DfAM) guidelines.
What if my data quality isn’t great?
We have strong partnerships with stakeholders across the additive manufacturing industry and can provide expert guidance on data management. Our team can help you develop best practices to improve your data quality.
What type of file uploads does Part Identification support?
Part Identification supports STL, STEP, .3MF, .zip, and native CAD files, among many other file formats.
Pictured: From the part list, you can see all of the parts that have been assessed with the Part Identification tool, get an overview of cost and lead time savings, and filter parts based on characteristics like technology and material.
How many files can I upload to Part Identification at a time?
Part Identification supports bulk file imports, allowing you to analyze large volumes of part data quickly.
What if I don’t have 3D files?
That's ok, we don't need it! We can process metadata to evaluate AM suitability.
Can Part Identification analyze 2D drawings?
Yes. Part Identification now offers ITAR-compliant 2D drawing analysis powered by artificial intelligence. Our software can extract data from 2D drawings (including those in different formats) and make initial technology assessments within seconds.
I don’t own the parts data. Can I still use Part Identification?
Yes! We can work with economic, inventory, or emissions data and connect with your parts supplier. Intellectual property is protected through end-to-end encryption.
How does Part Identification suggest material substitutes?
Our system includes a material database with over 1,300 materials. Based on your configuration, it can suggest material substitutes, ensuring access to the latest and most reliable data.
Can Part Identification suggest printing orientation?
Yes! Part Identification can suggest the best printing orientations to minimize printing time and support material waste or surface imperfections.
Pictured: After a part has been assessed and optimized for additive manufacturing, you can add it to the Catalog. This creates a central repository for organizations to collaborate on parts internally and securely share part files between approved users.
How do I demonstrate the value of Part Identification to management?
Part Identification drives significant cost and time savings by automating the analysis of large inventory datasets. It helps companies quickly identify high-value 3D printing opportunities, saving time and resources.
How much can I save using Part Identification?
Companies using Part Identification can save $5-$9 million annually by optimizing production costs, reducing warehouse operations expenses, and minimizing downtime. Streamlining part identification for 3D printing can also cut labor costs by over $60,000.
Frequently Asked Questions: 3YOURMIND Distributed Manufacturing
To browse FAQs about Distributed Manufacturing's order management module, jump here.
For FAQs about the MES portion of Distributed Manufacturing, click here.
What is 3YOURMIND Distributed Manufacturing?
3YOURMIND's Distributed Manufacturing is a manufacturing intelligence solution that automates on-demand ordering and part production. The software is suitable for organizations that manage inventories of spare parts, production parts, serial parts, and production tools like jigs and fixtures, as well as those producing their parts where consistent, repeatable quality is critical.
Distributed Manufacturing caters to both internal production facilities and contracted on-demand manufacturing services, ensuring smooth operations and high-quality output across various production environments.
Pictured: Distributed Manufacturing gives organizations an overview of all current orders in production, including information on customers, prices, technology, and print status.
How long does it take to implement Distributed Manufacturing?
With our standard templates, you can be operational the next day. With customized pricing formulas, you can go live in a week. However, more complex needs may take up to four weeks.
Is Distributed Manufacturing an off-the-shelf solution?
We offer a robust base product for core processes, with API and webhook integrations for customization. You can quickly upload parts and be operational, but we also support sophisticated workflows.
Are there customization options to fit my business needs?
We offer standard API integrations. However, if you need to integrate with specific software, we can customize it based on your unique needs.
How can I prepare my company for Distributed Manufacturing?
No specific preparation is needed for service bureaus already producing 3D-printed parts. We streamline operations and help increase efficiency.
For enterprises, having a clear understanding of pricing, defined roles, technologies, and IT architecture will ensure a smoother implementation.
Distributed Manufacturing (Order Management FAQs)
Pictured: Distributed Manufacturing makes it easy for users to get instant price quotes using your pricing formulas.
How does it calculate price quotes and delivery timelines?
Our system uses advanced 3D file processing algorithms to extract data for price calculations. Delivery timelines are based on customer-provided data and finishing times.
Can I use Distributed Manufacturing for prototyping?
Yes. Many organizations use it for prototyping. You can upload parts, get instant pricing, and receive feedback on printability. You can also iterate on files in your catalog.
Pictured: Part information is tracked throughout its entire lifecycle. Once a part is assessed in Part Identification, its data remains connected through ordering and production, creating a continuous record. This data thread supports quality control, such as in the event of material or part recalls.
Can I use Distributed Manufacturing to order parts from other contract manufacturers?
Yes. You can invite contract manufacturers to your platform and control their access. However, currently, 3YOURMIND platforms cannot connect directly. We expect this capability to be available in 2026.
Does Distributed Manufacturing integrate with other software solutions? Which ones?
Yes. We integrate with SAP, PTC CREO (for designers), 2D drawing digitization, and more. We also have tools for further software integration as needed.
Is it secure?
Yes, we operate on AWS Cloud and Microsoft Azure, with options for GovCloud or on-premise deployment. Enterprise-level security and encryption are built-in.
How does Distributed Manufacturing keep intellectual property secure?
We offer group and permissions controls to configure who can access specific parts and information.
Distributed Manufacturing (MES) FAQs
Is Distributed Manufacturing a classic MES solution?
We offer machine scheduling, shop floor monitoring, and seamless integration with our order management system. It also features customizable, flexible workflows.
Pictured: The schedule overview displays which machines are in production and for how long, helping companies optimize their workflows. It is also linked to the orders, giving customers real-time updates on their order status.
Can it schedule production orders based on machine availability?
Yes. You can define workstations and machines, add them to the system, and configure printers from our database of 30+ machines. You can view current jobs in production and identify available machines.
How does it schedule production orders?
Operators can manually schedule jobs, and the system suggests the next available slots. If a machine is occupied, it will recommend the next free time slot.
Does it integrate with Magics?
Yes. Many of our customers use Magics in their workflows. We can import nested jobs via CSV and schedule them in our MES.
Pictured: Machine operators can use Distributed Manufacturing to view material inventory across their entire fleet, making it easier to order and install print materials.
What machines does Distributed Manufacturing connect to?
We partner with more than 10 machine manufacturers and connect to more than 30 machines. To get the most up-to-date list, contact us and ask about machine connectivity.
What quality assurance or quality control functionalities does it offer?
We provide job documentation forms to record part quality and job parameters. We also integrate with Markforged printers to automatically receive build reports with sensor data.
Can I customize Distributed Manufacturing to fit my business?
Yes, you can create custom workflows for any technology or post-processing to fully support your operations, including outsourcing.
What standard machine connectivity protocols do you support?
We support OPC/UA, Umati (VDMA), and MQTT (used by companies like Ford).
General Questions
What's the difference between Part Identification and Distributed Manufacturing?
Part Identification is a solution used to scale additive manufacturing. It is often used by companies with extensive inventories of existing parts who want to understand how additive manufacturing fits into their larger part procurement strategy.
Part Identification enables enterprise companies to:
- Centralize and standardize data
- Digitize parts and store them in a digital part catalog
- Assess new or existing parts for AM compatibility
Distributed Manufacturing, on the other hand, serves organizations that produce qualified parts for additive manufacturing and need a software workflow to produce those parts more efficiently and with better quality.
Distributed Manufacturing helps to:
- Manage price quotes and part orders
- Distribute and track production
- Unlock data insights for better decision-making
How do I know if my company is mature enough for additive manufacturing?
That depends on your goals. The first part of the equation is to answer whether additive manufacturing would benefit your organization's operations.
The benefits of additive manufacturing tend to fall into two categories: the design of new AM-first parts or re-engineering existing parts for AM
Additive manufacturing offers freedom of design, which is excellent for original equipment manufacturers who want to speed up the time to market by using 3D printing to test and prototype parts.
Additive manufacturing also benefits organizations that need to sustain equipment but often experience long lead times to get replacement spare parts from the traditional manufacturing supply chain.
It is crucial to be clear about your organization's goals and define the role additive manufacturing will play in your operations. We recommend Part Identification for organizations that want to first explore the potential of 3D printing with their current inventory.
For companies looking to purchase their first industrial 3D printer, we recommend booking a free consultation with EOS and asking for a Rapid Part Identifier. This way, you can see your part's AM potential before purchasing a machine.
See the software in action. Request a free consultation.