End-to-End Management Software in Additive Manufacturing
Since its introduction in 1988, Microsoft Office has reshaped the way we work. Graphic designers, engineers and office managers now have everything they need in a complete software package. What’s the common link between software companies like Microsoft, Adobe, Autodesk and Siemens?
The Birth of End-to-End Software:
Microsoft Unleashes The Suite
Each company has chosen a user group and provided them with a complete software suite of solutions for a specific daily workflow. Adobe covers the entire design industry’s needs - graphics, photos and videos, special effects and more. Autodesk can support each type of 3D graphic design, from architecture to animation to product simulation; Siemens’ focus is on design for production, touching on simulation, cost calculation, design iterations and production planning.
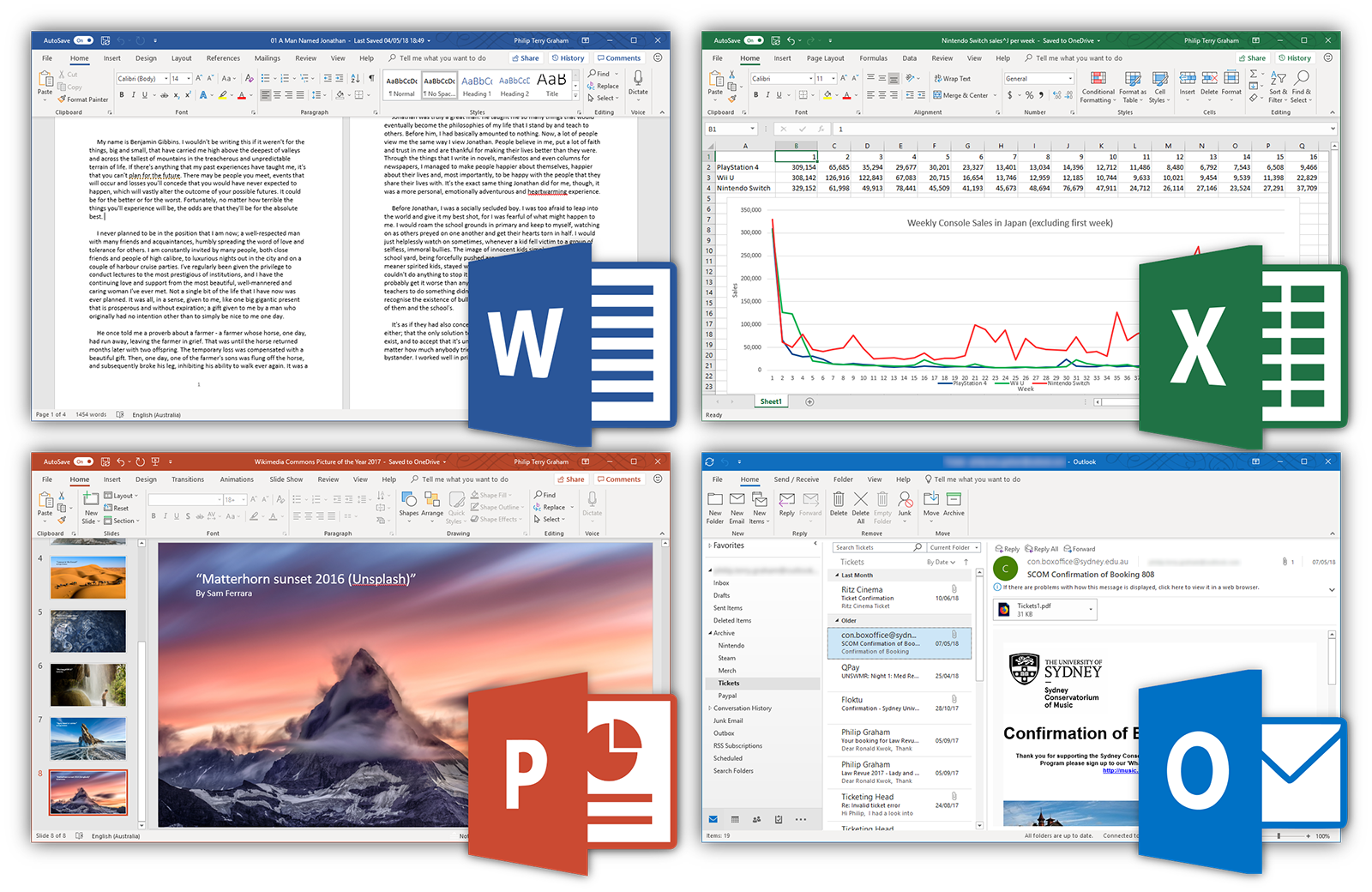
Even though not all functionalities are available from the same user interface, after gaining experience in one of the available programs, it’s much simpler to get used to the other software modules within the same suite. More important, however, is the data can be quickly and easily transferred within the suite - between departments and user roles - with a minimum of friction. This brings tremendous value to companies - especially at scale and over time.
What’s the learning curve for a new employee coming into a new team? Every on-boarding process requires an investment of time, both from the employee and their manager. This generates hidden costs often not considered during the software purchasing process. When processes and the number of systems are simplified, the ramp-up process can also be significantly shortened.
In today’s world we’re often forced to use a huge number of different software tools. In most cases, our internal communication is covered by at least two different systems - one for asynchronous communication and a second for an instant, synchronous one. Creating reports, managing projects, creating documentation... each has its specific tools. It adds up to a very complicated working environment.
This is the advantage that an end-to-end workflow offers. Less steps, less confusion, less potential for error. Companies who created these interlinked suites have stood the test of time by becoming a default standard in software for specific user groups.
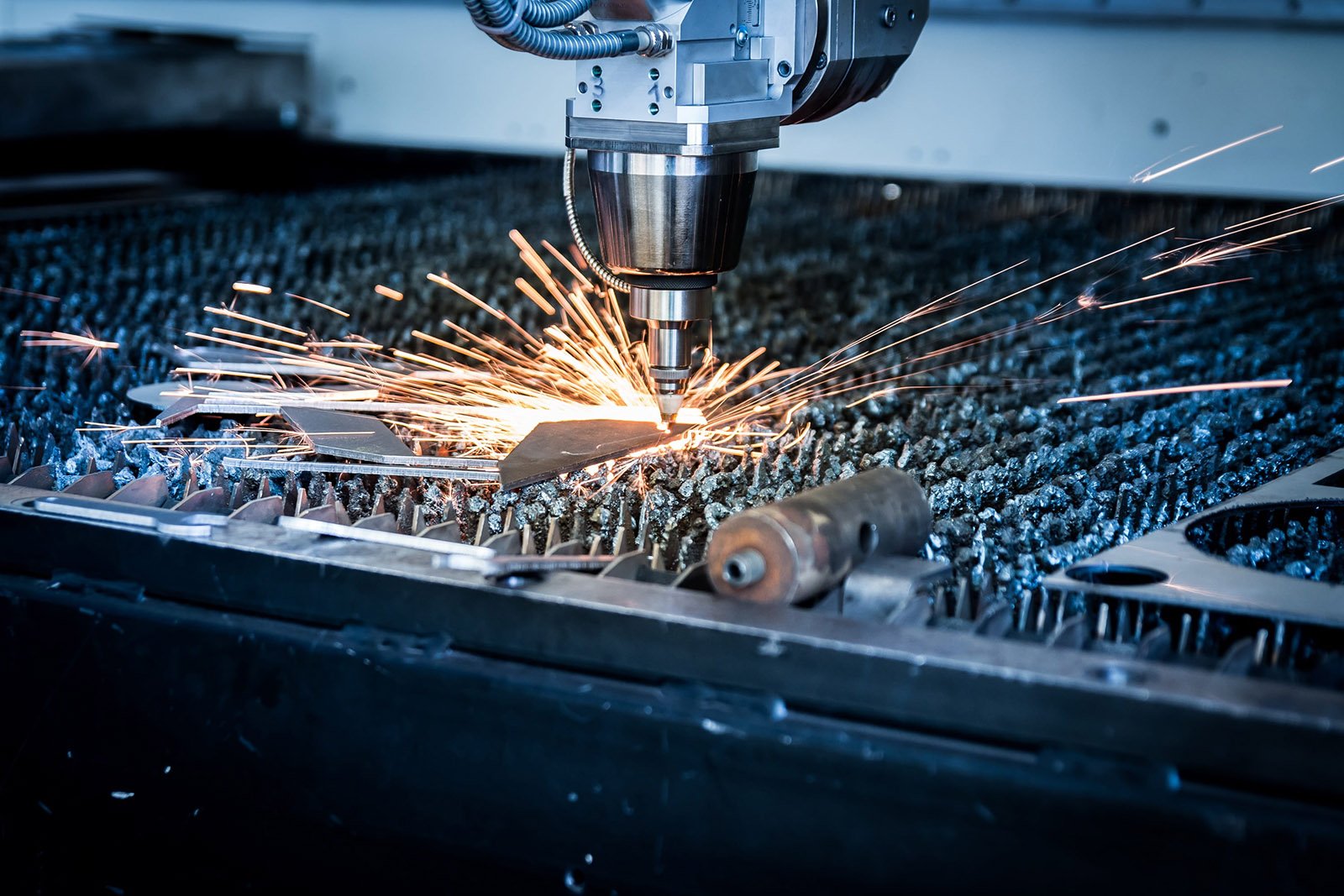
Removing Variables in Production:
A Guarantee of Quality
The case for end-to-end software, then, seems like an open and shut case. But how does the concept fit with hardware?
Let’s assume we’re trying to set up a production line with robots and CNC manufacturing centers. It wouldn’t be possible to find just one supplier for both types of machines in all variations we need, but we’d still try to stay with the lowest number of different providers as possible. We might even hire a consultant to recommend configurations that will provide the most stability between vendors. Why would we do that?
Ease of use is just one of many aspects that contribute to a successful production line. The truth is that machines require constant maintenance. Each item of hardware requires staff training on proper use and maintenance. By having a low variety of machine types and manufacturers we are limiting the complexity of shop floor management.
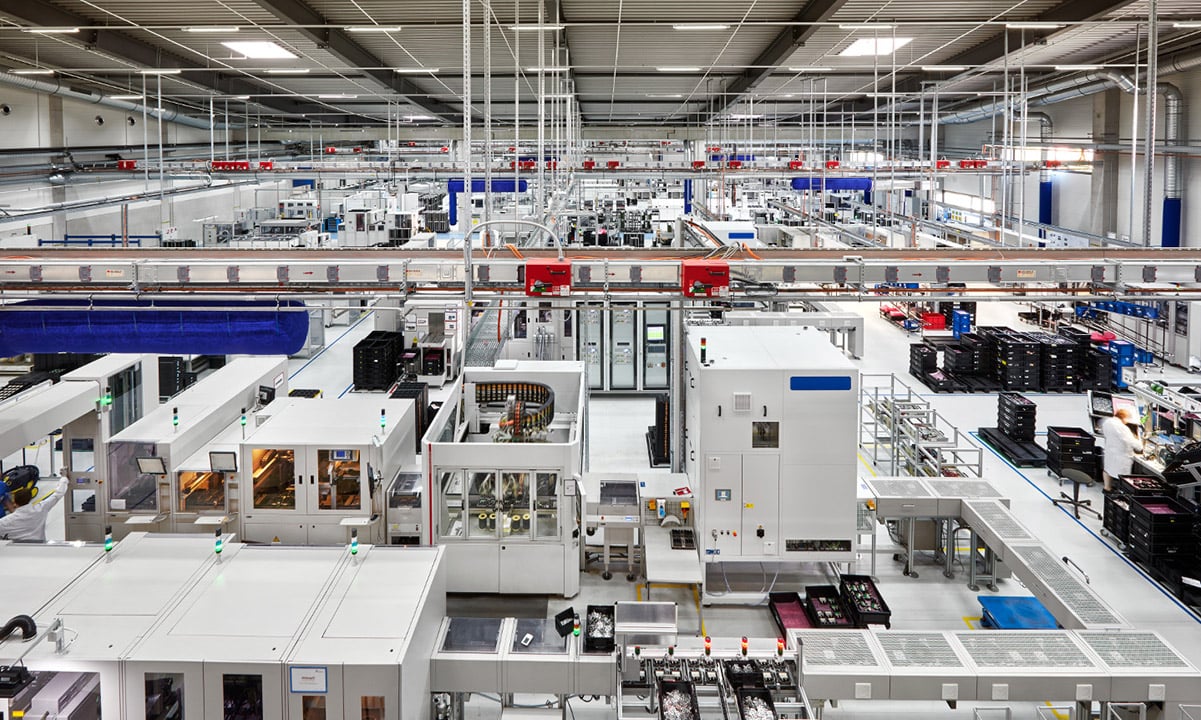
The second aspect is reducing contact points. When a vendor’s mechanic comes for maintenance, they can check all machines on the production floor in a single visit. There’s a relationship built up over time, including knowledge of the processes and goals within each company. And if that person needs to change their production system, it means connecting with just one new vendor or integrator.
Finally, production requires quality and consistency. This can often be achieved only by trial-and-error production on machines until the quality targets are reached. The time investment required may result in first products having no tangible quality increase.
The overall stability of a company or service provider is far more valuable than instant functionality. Supporting bigger solutions with a wider product range and longer experience in accomplishing your goals - even if you pay a premium up-front - can be the wiser investment in the long run.
In both software and hardware, it’s likely that during the purchasing process, bigger companies will focus on a limited number of suppliers. Choosing a package that covers a larger percentage of products needs to be negotiated to the lowest price with a wide variety of vendors.
Shorter Production or Faster Time-to-Market:
Which Offers More Value?
Additive Manufacturing has its own unique characteristics. We don’t need to build product-specific production lines: we need to build process-specific production lines.
Many leading industrial production companies are creating 3D printing centers (competency centers) to boost the way additive manufacturing processes are perceived in their company. It’s no longer the case that companies have to wait months to try new product prototypes. Designers can now iterate hundreds of times during the design process to optimize ideas and get to production faster.
But access to prototyping services are only as good as the pathways. We have seen a significant shift in companies focusing on AM production switching to an end-to-end suite that includes the design process. Additive Manufacturing offers the chance to remain in the same production technology: from prototyping to functional test parts and into series production. The longer companies are staying in additive technologies, the more value is generated by a single, end-to-end software solution.
Prototyping is no longer the only way AM is used in the production line. We are seeing a steadily increasing number of applications of additive manufacturing in high volume production. AM has a higher need for data tracking and dynamically shifting production. Unfortunately most existing MES systems are not built for the types of processing, file analysis and parameters that affect additive. That leaves even leading manufacturers opting to price and schedule using manual processes (eg. excel sheets) rather than software.
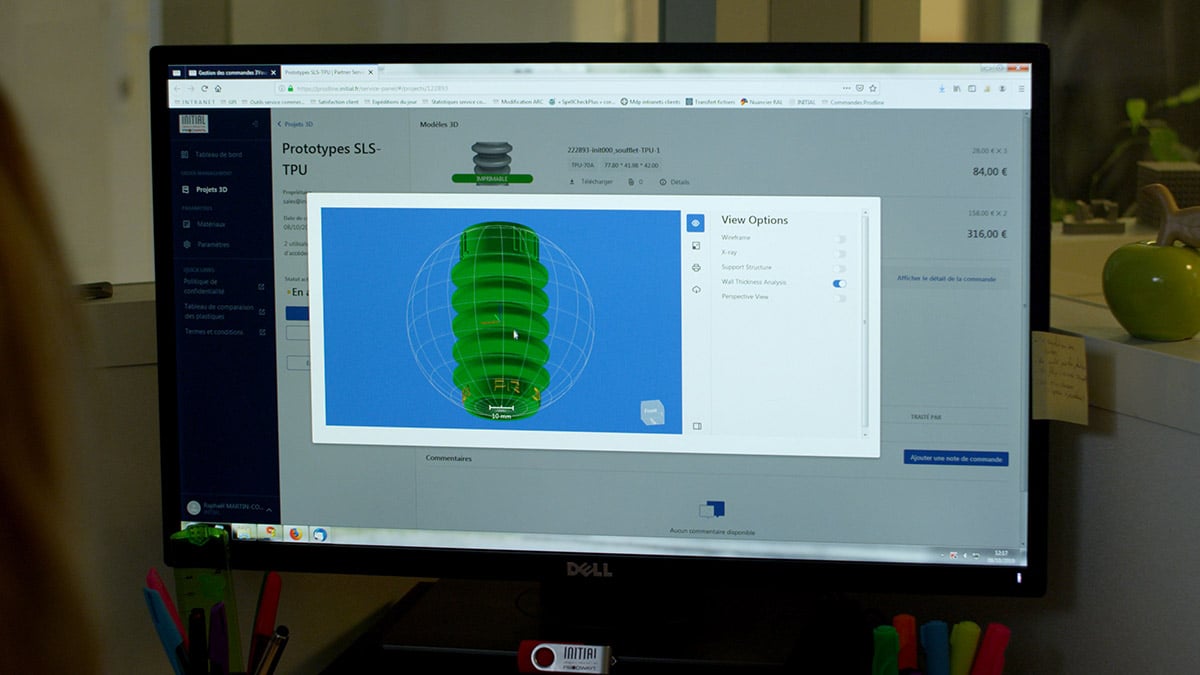
The result is a strong pivot in the industrial market towards complete additive manufacturing workflow software. This allows the customer to build a continuous, streamlined pathway: from AM part analysis, automated quoting and the production itself. The production engineers can automate routine paperwork and use transparent 3D data management for production planning and tracking. All processes can be accomplished without opening third party tools.
As we saw above, the value to an individual employee for working in a single system is high. The advantage that large companies and service bureaus receive can make the difference between a flop or success story.
Getting to Genuine Agile Manufacturing:
What Will it Take?
Every time an internal working environment evolves, employees have to adjust to keep up and rebuild the position in the market. Agile Manufacturing requires a new mentality for agile production and process management. It is now possible to produce dramatically different products in the same machine run. But the distribution and further processing of those parts needs to be dynamically managed and scheduled. This requires accurate, streamlined data flow, which is the biggest strength of end-to-end workflow software.
Process automation is the second stage of keeping up with the pace of change in modern manufacturing. There are plenty of software solutions available to manage your customer database, create invoices, track your warehouse stock, plan production. Most of them may already be used in your company. The issue with these is that when the data is isolated in separate products, there’s no way to establish proper communication between them. The options are either manual transfer with risk of a human mistake, or shifting to a complete software solution.
This will be the next major software driver in additive manufacturing.
Biography: Jakub Karkocha
Jakub (Kuba) Karkocha is the Technical Consultant Manager for 3YOURMIND.
He has held this position for four years, acting as a lead consultant for additive manufacturing projects with large OEMs and leading 3D printing services. He has delivered AM produced parts, optimized 3D files, AM project roll-out strategies and pricing algorithms for 3D printing bureaus. Since 2018, he has also led the deep technology squad who improved the printability analysis algorithms and developed an orientation optimization and pricing specifically for additive manufacturing. He also serves as the in-house 3D printing technologies specialist pulling from his experience analyzing surface quality of various additive technologies at the Wroclaw University of Science and Technology.